Flotation is a complex process with many variables
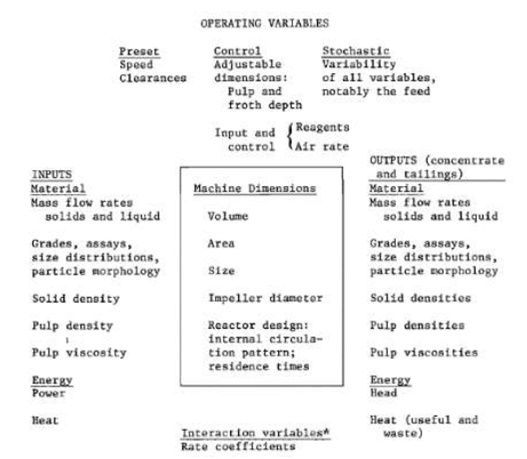
(Harris,
C C, 1975. Flotation Machines, in Flotation, ed. M.C.
Fuerstenau, pp 753-815 AIME: New York)
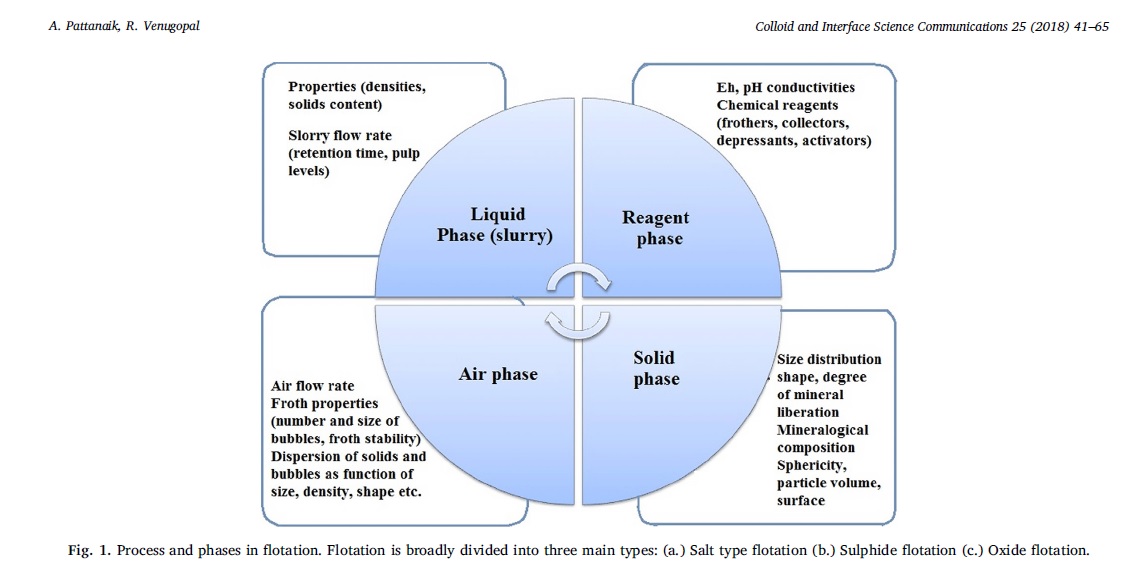
Particle
shape is one of the affecting variables on the
particle-bubble attachment
Ore grinding in froth flotation is an important step to
liberate the valuable mineral particles from the gangue
(Forssberg
et al., 1993).
When considering particle shape in minerals processing,
comminution is of particular interest as this is the
process where the particles attain their shape which in
turn affects classification and separation stages
downstream. Studying the shape characteristics of
progeny particles can also be used to interpret breakage
mechanisms within milling devices and in some instances,
can even be related to the degree of liberation (Leroy
et al., 2011).
Particle shape can have an impact on numerous processes
through its effect on drag coefficients, rheology, and
particle bubble interactions.
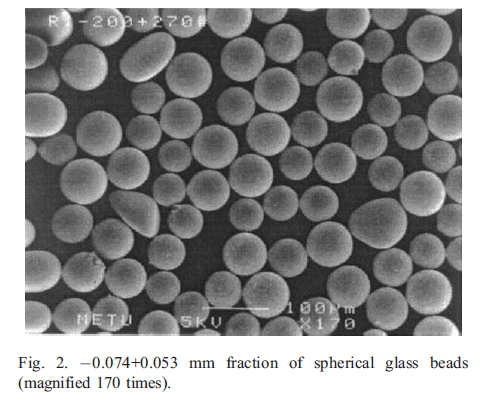
Froth flotation is a separation process which plays a
major role in the mining industry. The flotation process
essentially relies on the attachment of solid particles
on the surface of gas bubbles immersed in water.
The attachment of a solid particle on the surface of a
gas bubble can be divided into three successive stages:
the particle approach, the collision with the bubble and
the sliding down the gas–bubble interface (Schulze,
1989; Albijanic et al., 2010).
The downward sliding motion of the particle is caused by
the gravity and also by the hydrodynamic forces arising
from the local water flow around the rising bubble.
Should the particle approach the bubble surface within
the range of attractive surface forces, a thin
intervening liquid film between the gas–liquid interface
and the solid–liquid interface forms. The liquid film
eventually drains, leading to a critical thickness at
which rupture occurs (Ralston
et al., 1999). The
rupture of the liquid film results in the formation of a
stable three-phase contact (Schulze,
1992).
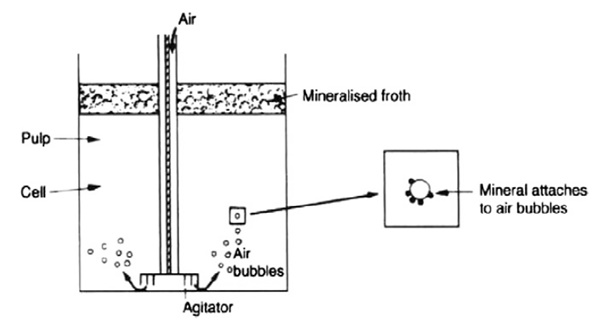
Figure 1. The fact that the recovery of particles by true
flotation is influenced by also particle shape has been
widely reported by some researchers
(Koh et al., 2009; Vizcarra et al., 2011; Ulusoy and
Yekeler, 2005).
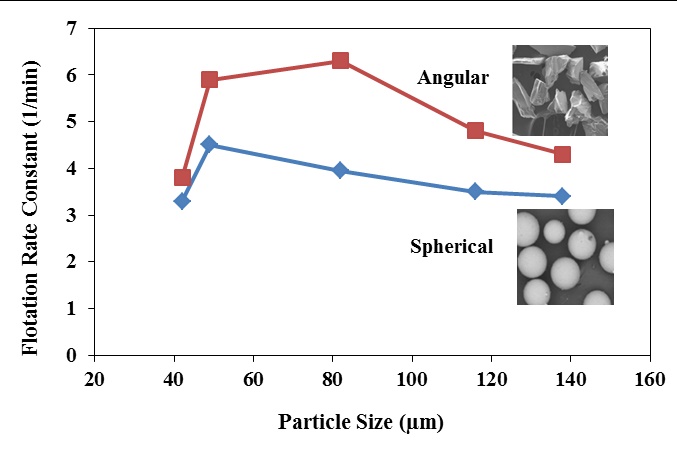
Figure 2. Flotation rate as a function of particle size
for angular and spherical particles (Adapted from
Koh et al. (2009).
Koh, P.T.L., Hao, F.P., Smith, L.K.,
Chau, T.T. and Bruckard, W.J., 2009. The effect of
particle shape and hydrophobicity in flotation.
International Journal of Mineral Processing 93(2),
128-134. |