You have a hypothesis, you do an
experiment, and then you either
confirm your initial idea or you
don’t. But for me, that’s less of a
challenge and more of a learning
opportunity for the next project.
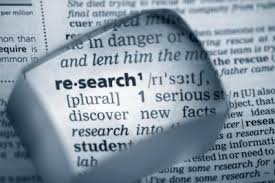
Research
is an active, diligent and
systematic process of inquiry in
order to discover, interpret or
revise facts, events, behaviors or
theories, or to make practical
applications with the help of such
facts, laws or theories.
We are building
toward a future that centers on
collaboration—on breaking down
barriers and working together across
distances, across disciplines, and
across institutions and
organizations for the good of
science.
Major Research Interest
“Raw
materials
including minerals
and metals to make electric vehicles,
batteries, wind turbines, and solar
panels, are at the heart of the
green deal since the energy
transition is a switch from fossil
fuels to metals. Therefore, the
demand for minerals, which are
essential to the growth and
maintenance of civilization, is
rising for the global energy
transition. Since the majority of
mined ores need to be processed
before being turned into usable
metals or finished mineral
commodities, mineral processing,
which is the use of physical or
chemical means (gravity separation,
magnetic separation, flotation,
electrostatic separation, leaching,
etc.) to process ores, makes
contributions to all areas of
technology regards to scientific
concepts, engineering principles,
products, and processing. In other
words, the chemical industry,
municipal and industrial waste
treatment, and recycling, heavily
utilize mineral processing
technologies. Moreover, metal
recycling—the process of turning
scrap metal into new metal products—should
be practiced to lower greenhouse gas
emissions, protect natural resources,
and control energy usage. A good
waste collection system, separation
and classification processes, and
measures have been started to be
taken in the world to encourage the
metal recycling industry. As a
result, mineral processing,
particularly extractive metallurgy,
which has been disregarded for years,
has begun to assume a crucial role
in the electrification of the world.”
Ore
grinding in froth flotation is
an important step to liberate the
valuable mineral particles from the
gangue (Forssberg et al., 1993).
When considering particle shape in
minerals processing, comminution is
of particular interest as this is
the process where the particles
attain their shape which in turn
affects classification and
separation stages downstream.
Studying the shape characteristics
of progeny particles can also be
used to interpret breakage
mechanisms within milling devices
and in some instances, can even be
related to the degree of liberation
(Leroy et al., 2011). Particle shape
can have an impact on numerous
processes through its effect on drag
coefficients, rheology, and particle
bubble interactions.
Powders are used
extensively across a wide range of
industries- they possess many
valuable properties and benefits.
However, they are also challenging
materials with bulk flow properties
that are difficult to predict, even
within simple process operations.
They change their behavior and
performance depending on their
environment- conditions, etc. Poor
understanding of a powder's behavior
in response to these behaviors can
lead to production stoppages,
inefficiency and poor quality or out
of spec products.
Though flotation
was first used in the early 1900s
and has undergone extensive research
and development, it is still not
fully understood and is still
comparatively ineffective. Because
the flotation process, which is
actually fairly complex, is
influenced by roughly 100 different
factors. Additionally, it makes
control more difficult due to the
frequent interactions between the
flotation factors and the
complicated, non-linear correlations
among the several factors. Although
it might not be essential to
manipulate or measure each of these
variables at the same time in order
to get excellent process control
results, each of these factors and
how they affect the flotation
procedure should be taken into
account. In this context, it is
suggested that particle properties
(size distribution, shape, degree of
mineral liberation) are among the
most important factors, especially
from the point of view of advanced
flotation control and optimizing
flotation control.
Currently working to
decode the relationships between
particle geometry and unit
operations in ore preparation, such
as grinding and flotation
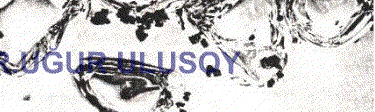
1. |
Effect of grinding on
particle morphology by image
analysis |
2. |
Effect of particle shape on
concentration of industrial
mineral particles |
3. |
Flotation, particle-bubble
adhesion and wetting,
column flotation, |
4. |
Particle characterization
(shape, surface roughness, shape
factor). |
5. |
Coal
washing and optimization of the
DM circuits |
6. |
Flocculation
and agglomeration |
7. |
Effect of ultrasound on
the flotation |
8. |
Dynamic
image analysis of particles in
mineral processing appliations |
Skills
•Contact
Angle Measurements
•Wettability
•Mineral
Processing
•Material
Characterization
•Hydrophobicity
•Contact
Angle
•Particle
Size Analysis
•Flotation
•Shape
Analysis
•Particle
surface roughness
•Grinding
•Sieving
•Surtronic
3+
surface roughness meter
•Particle
Size
•Hallimond
tube
•Microflot
flotation test
•Gamma
flotation
•Ultrasound
•Image
Analysis
•Particle
Technology
•Mineral
Characterization
•Surface
Characterization
•Dynamic
image analysis
•E-waste
recycling
•Metal
recovery
Our mission is to
drive success by helping to build a
more sustainable, technology-enabled
future for all.